Torsion on Expansion Joints in Piping Systems
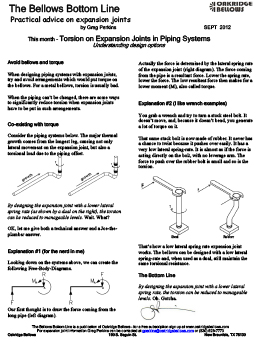
Torsion on Expansion Joints in Piping Systems
Understanding design
Avoid bellows and torque
When designing piping systems with expansion joints, try and avoid arrangements which would put torque on the bellows.
For a metal bellows, torsion is usually bad.
When the piping can’t be changed, there are some ways to significantly reduce torsion when expansion joints have to be put in such arrangements.
Co-existing with torque
Consider the piping systems below. The major thermal growth comes from the longest leg,
causing not only lateral movement on the expansion joint, but also a torsional load due to the piping offset.
By designing the expansion joint with a lower lateral spring rate (as shown by a dual on the right),
the torsion can be reduced to manageable levels. Wait. What?
OK, let me give both a technical answer and a Joe-the- plumber answer.
Explanation #1 (for the nerd in me)
Looking down on the systems above, we can create the following Free-Body-Diagrams.
Our first thought is to draw the force coming from the long pipe (left diagram).
Actually the force is determined by the lateral spring rate of the expansion joint (right diagram).
The force coming from the pipe is a resultant force. Lower the spring rate, lower the force.
The low resultant force then makes for a lower moment (M), also called torque.
Explanation #2 (I like wrench examples)
You grab a wrench and try to turn a stuck steel bolt. It doesn’t move, and, because it doesn’t bend, you generate a lot of torque on it.
That same stuck bolt is now made of rubber. It never has a chance to twist because it pushes over easily.
It has a very low lateral spring-rate. It is almost as if the force is acting directly on the bolt, with no leverage arm.
The force to push over the rubber bolt is small and so is the torsion.
That’s how a low lateral spring rate expansion joint works. The bellows can be designed with a low lateral spring-rate and,
when used as a dual, still maintain the same torsional resistance.
The Bottom Line
By designing the expansion joint with a lower lateral spring rate, the torsion can be reduced to manageable levels. Oh. Gotcha.