The Heartache of Thermal Shock
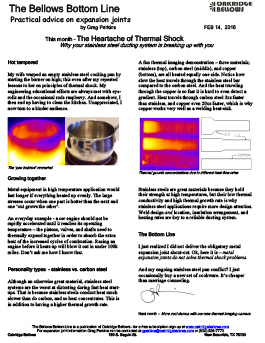
Why your stainless steel ducting system is breaking up with you
Hot tempered
My wife warped an empty stainless steel cooking pan by starting the burner on high; this even after my repeated lessons to her on principles of thermal shock. My engineering educational efforts are always met with eyerolls and the occasional rude raspberry. And somehow, I then end up having to clean the kitchen. Unappreciated, I now turn to a kinder audience.
Growing together Metal equipment in high temperature application would last longer if everything heated up evenly. The large stresses occur when one part is hotter than the next and one ‘out grows the other’.
An everyday example – a car engine should not be rapidly accelerated until it reaches its operating temperature – the pistons, valves, and shafts need to thermally expand together in order to absorb the extra heat of the increased cycles of combustion. Racing an engine before it heats up will blow it out in under 100k miles. Don’t ask me how I know that.
Personality types – stainless vs. carbon steel
Although an otherwise great material, stainless steel systems are the worst at distorting during fast heat startups. That is because stainless steels conduct heat much slower than do carbon, and so heat concentrates. This is in addition to having a higher thermal growth rate.
A fun thermal imaging demonstration – three materials; stainless (top), carbon steel (middle), and copper (bottom), are all heated equally one side. Notice how slow the heat travels through the stainless steel bar compared to the carbon steel. And the heat traveling through the copper is so fast it is hard to even detect a gradient. Heat travels through carbon steel 3xs faster than stainless, and copper even 20xs faster, which is why copper works very well as a welding heat-sink.
Stainless steels are great materials because they hold their strength at high temperatures, but their low thermal conductivity and high thermal growth rate is why stainless steel applications require more design attention. Weld design and location, insulation arrangement, and heating rates are key to a reliable ducting system.
The Bottom Line
I just realized I did not deliver the obligatory metal expansion joint shout-out. Ok, here it is – metal expansion joints do not solve thermal shock problems. And my ongoing stainless steel pan conflict? I just occasionally buy a new set of cookware. It’s cheaper than marriage counseling.