Metal Bellows Cycle Life – EJMA vs ASME
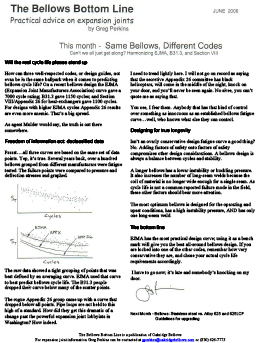
Will the real cycle life please stand up
How can three well-respected codes, or design guides, not even be in the same ballpark when it comes to predicting bellows cycle life? On a recent bellows design the EJMA (Expansion Joint Manufacturers Association) curve gave a 7000 cycle rating; B31.3 gave 1150 cycles; and Section VIII/Appendix 26 for heat-exchangers gave 1100 cycles. For designs with higher EJMA cycles Appendix 26 results are even more anemic. That’s a big spread.
As agent Mulder would say, the truth is out there somewhere.
Freedom of information act: declassified data
Psssst….all three curves are based on the same set of data points. Yep, it’s true. Several years back, over a hundred bellows grouped from different manufacturers were fatigue tested. The failure points were compared to pressure and deflection stresses and graphed.
The raw data showed a tight grouping of points that was best defined by an averaging curve. EJMA used that curve to best predict bellows cycle life. The B31.3 people dropped their curve below many of the scatter points.
The rogue Appendix 26 group came up with a curve that dropped below all points. Pipe loops are not held to this high of a standard. How did they get this dramatic of a change past the powerful expansion joint lobbyists in Washington? How indeed.
I need to tread lightly here. I will not go on record as saying that the secretive Appendix 26 committee has black helicopters, will come in the middle of the night, knock on your door, and you’ll never be seen again. No siree, you can’t quote me as saying that.
You see, I fear them. Anybody that has that kind of control over something as innocuous as an established bellows fatigue curve…well, who knows what else they can control.
Designing for true longevity
Isn’t an overly conservative design fatigue curve a good thing? No. Adding factors of safety onto factors of safety compromises other design considerations. A bellows design is always a balance between cycles and stability.
A longer bellows has a lower instability or buckling pressure. It also increases the number of long-seam welds because the coil of material is no longer wide enough for a single seam. As cycle life is not a common reported failure mode in the field, these other factors should bear more attention.
The most optimum bellows is designed for the operating and upset conditions, has a high instability pressure, AND has only one long-seam weld.
The bottom line
EJMA has the most practical design curve; using it as a bench mark will give you the best all-around bellows design. If you are locked into one of the other codes, remember how very conservative they are, and chose your actual cycle life requirements accordingly.
I have to go now; it’s late and somebody’s knocking on my door.