Improving Protective Covers
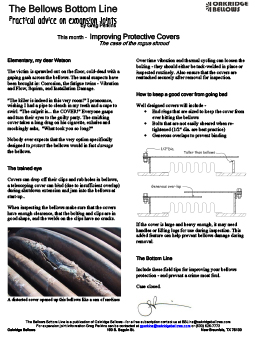
Elementary, my dear Watson
The victim is sprawled out on the floor, cold-dead with a gaping gash across the bellows. The usual suspects have been brought in: Corrosion, the fatigue twins – Vibration and Flow, Squirm, and Installation Damage.
“The killer is indeed in this very room!” I pronounce, wishing I had a pipe to clench in my teeth and a cape to swirl. “The culprit is… the COVER!” Everyone gasps and turn their eyes to the guilty party. The smirking cover takes a long drag on his cigarette, exhales and mockingly asks, “What took you so long?”
Nobody ever expects that the very option specifically designed to protect the bellows would in fact damage the bellows.
The Trained Eye
Covers can drop off their clips and rub holes in bellows, a telescoping cover can bind (due to insufficient overlap)
during shutdown extension and jam into the bellows at start-up..
When inspecting the bellows make sure that the covers have enough clearance, that the bolting and clips are in good shape, and the welds on the clips have no cracks.
A distorted cover opened up this bellows like a can of sardines
Over time vibration and thermal cycling can loosen the bolting – they should either be tack-welded in place or inspected routinely. Also ensure that the covers are reattached securely after removal for inspection.
How to keep a good cover from going bad?
Well designed covers will include:
– End rings that are sized to keep the cover from ever hitting the bellows
– Bolts that are not easily sheared when retightened (1/2″ dia. are best practice)
– Generous overlaps to prevent binding
If the cover is large and heavy enough, it may need handles or lifting lugs for use during inspection. This added feature can help prevent bellows damage during removal.
The Bottom Line
Include these field tips for improving your bellows protection – and prevent a crime most foul. Case closed.