The International Dispute over Multi-Ply Bellows
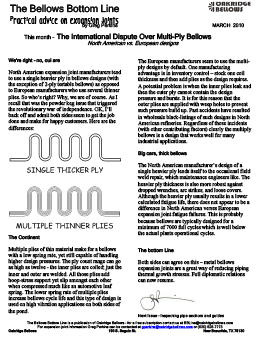
We’re right – no, oui are
North American expansion joint manufacturers tend to use a single heavier ply in bellows designs (with the exception of 2-ply testable bellows) as opposed to European manufacturers who use several thinner plies. So who’s right? Why, we are of course. As I recall that was the powder keg issue that triggered the revolutionary war of independence. OK, I’ll back off and admit both sides seem to get the job done and make for happy customers. Here are the differences:
The Continent
Multiple plies of thin material make for a bellows with a low spring rate, yet still capable of handling higher design pressures. The ply count range can go as high as twelve – the inner plies are coiled; just the inner and outer are welded. All those plies add hoop-stress support yet slip amongst each other when compressed much like an automotive leaf spring. The lower spring rate of multiple plies increase bellows cycle life and this type of design is used on high vibration applications on both sides of the pond.The European manufacturers seem to use the multi- ply designs by default. One manufacturing advantage is in inventory control – stock one coil thickness and then add plies as the design requires. A potential problem is when the inner plies leak and then the outer ply cannot contain the design pressure and bursts. It is for this reason that the outer plies are supplied with weep holes to prevent such pressure build up. Past accidents have resulted in wholesale black-listings of such designs in North American refineries. Regardless of those incidents (with other contributing factors) clearly the multiply bellows is a design that works well for many industrial applications.
Big cars, thick bellows
The North American manufacturer’s design of a single heavier ply lends itself to the occasional field weld repair, which maintenance engineers like. The heavier ply thickness is also more robust against dropped wrenches, arc strikes, and loose covers. Although the heavier ply usually results in a lower calculated fatigue life, there does not appear to be a difference in North American verses European expansion joint fatigue failures. This is probably because bellows are typically designed for a minimum of 7000 full cycles which is well below the actual plants operational cycles.
The bottom Line
Both sides can agree on this – metal bellows expansion joints are a great way of reducing piping thermal growth stresses. Full diplomatic relations can now resume.