Best Practices On Fillet Welding
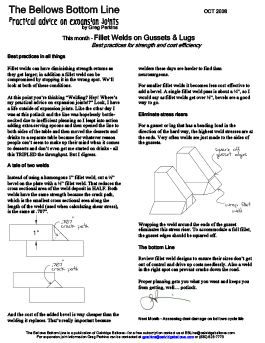
Best practices in all things
Fillet welds can have diminishing strength returns as they get larger; in addition a fillet weld can be compromised by stopping it in the wrong spot. We’ll look at both of these conditions.
At this point you’re thinking “Welding? Hey! Where’s my practical advice on expansion joints!?” Look, I have a life outside of expansion joints. Like the other day I was at this potluck and the line was hopelessly bottle-necked due to inefficient planning so I leapt into action adding extra serving spoons and then opened the line to both sides of the table and then moved the desserts and drinks to a separate table because for whatever reason people can’t seem to make up their mind when it comes to desserts and don’t even get me started on drinks – all this TRIPLED the throughput. But I digress.
A tale of two welds
Instead of using a humongous 1” fillet weld, cut a ½” bevel on the plate with a ½” fillet weld. That reduces the cross sectional area of the weld deposit in HALF. Both welds have the same strength because the crack path, which is the smallest cross sectional area along the length of the weld (used when calculating shear stress), is the same at .707”.
And the cost of the added bevel is way cheaper than the welding it replaces. That’s really important because welders these days are harder to find than neurosurgeons.
For smaller fillet welds it becomes less cost effective to add a bevel. A single fillet weld pass is about a ¼”, so I would say as fillet welds get over ½”, bevels are a good way to go.
Eliminate stress risers
For a gusset or lug that has a bending load in the direction of the hard way, the highest weld stresses are at the ends. Very often welds are just made to the sides of the gussets.
Wrapping the weld around the ends of the gusset eliminates this stress riser. To accommodate a full fillet, the gusset edges should be squared off.
The bottom Line
Review fillet weld designs to ensure their sizes don’t get out of control and drive up costs needlessly. Also a weld in the right spot can prevent cracks down the road.
Proper planning gets you what you want and keeps you from getting, well… potluck.