Metal vs Fabric Ducting Expansion Joint
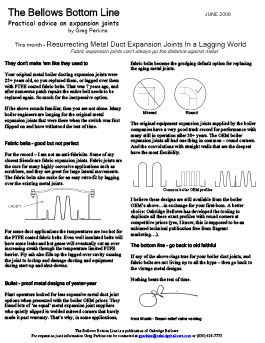
They don’t make ‘em like they used to
Your original metal boiler ducting expansion joints were 25+ years old, so you replaced them, or lagged over them with PTFE coated fabric belts. That was 7 years ago, and after numerous patch repairs the entire belt needs to be replaced again. So much for the inexpensive option.
If the above sounds familiar, then you are not alone. Many boiler engineers are longing for the original metal expansion joints that were there when the switch was first flipped on and have withstood the test of time.
Fabric belts – good but not perfect
For the record – I am not an anti-fabricite. Some of my closest friends are fabric expansion joints. Fabric joints are the cure for many highly corrosive applications such as scrubbers, and they are great for large lateral movements. The fabric belts also make for an easy retro-fit by lagging over the existing metal joints.
For some duct applications the temperatures are too hot for the PTFE coated fabric belts. Even well insulated belts will have some leaks and hot gases will eventually cut an ever increasing swath through the temperature limited PTFE barrier. Fly ash also fills up the lagged over cavity causing the joint to lockup and damage ducting and equipment during start-up and shut-downs.
Bullet – proof metal designs of yester-year
Plant operators looked for less expensive metal duct joint options when presented with the boiler OEM prices. They found lots of ‘as equal’ metal expansion joint suppliers who quietly slipped in welded mitered corners that barely made it past warranty. That’s why, in some applications, fabric belts became the grudging default option for replacing the aging metal joints.
Mitered Round
The original equipment expansion joints supplied by the boiler companies have a very good track record for performance with many still in operation after 30+ years. The OEM boiler expansion joints all had one thing in common – round corners. And the convolutions with straight walls that are the deepest have the most flexibility.
Common boiler OEM profiles
I believe these designs are still available from the boiler OEM’s above…in exchange for your first-born. A better choice: Oakridge Bellows has developed the tooling to duplicate all these exact profiles with round corners at competitive prices (yes, I know, this is supposed to be an unbiased technical publication free from flagrant marketing…).
The bottom line – go back to old faithful
If any of the above rings true for your boiler duct joints, and fabric belts are not living up to all the hype – then go back to the vintage metal designs.
Nothing beats the test of time.