Piping System Reliability
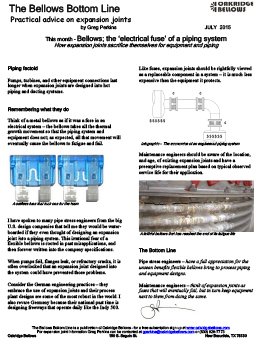
Piping factoid
Pumps, turbines, and other equipment connections last longer when expansion joints are designed into hot piping and ducting systems.
Remembering what they do
Think of a metal bellows as if it was a fuse in an electrical system – the bellows takes all the thermal growth movement so that the piping system and equipment does not; as expected, all that movement will eventually cause the bellows to fatigue and fail.
A selfless fuse that took one for the team
I have spoken to many pipe stress engineers from the big U.S. design companies that tell me they would be waterboarded if they even thought of designing an expansion joint into a piping system.
This irrational fear of a flexible bellows is rooted in past misapplications, and then forever written into the company specifications.
When pumps fail, flanges leak, or refractory cracks, it is often overlooked that an expansion joint designed into the system could have prevented those problems.
Consider the German engineering practices – they embrace the use of expansion joints and their process plant designs are some of the most robust in the world. I also revere Germany because their national past time is designing freeways that operate daily like the Indy 500.
Like fuses, expansion joints should be rightfully viewed as a replaceable component in a system – it is much less expensive than the equipment it protects.
Infographic – The economics of an engineered piping system
Maintenance engineers should be aware of the location, and age, of existing expansion joints and have a preemptive replacement plan based on typical observed service life for their application.
A faithful bellows that has reached the end of its fatigue life.
The Bottom Line
Pipe stress engineers – have a full appreciation for the unseen benefits flexible bellows bring to process piping and equipment designs.
Maintenance engineers – think of expansion joints as fuses that will eventually fail, but in